IIoT 應(yīng)用程序正在生成比以往更多的數(shù)據(jù)。在許多工業(yè)應(yīng)用中,尤其是位于偏遠(yuǎn)地區(qū)的高度分布式系統(tǒng),可能無(wú)法將大量原始數(shù)據(jù)不斷發(fā)送到中央服務(wù)器。為了減少延遲、降低數(shù)據(jù)通信和存儲(chǔ)成本并提高網(wǎng)絡(luò)可用性,企業(yè)正在將人工智能和機(jī)器學(xué)習(xí)轉(zhuǎn)移到邊緣,以便在現(xiàn)場(chǎng)進(jìn)行實(shí)時(shí)決策和行動(dòng)。
這些在物聯(lián)網(wǎng)基礎(chǔ)設(shè)施上部署人工智能能力的應(yīng)用被稱(chēng)為“AIoT”。盡管用戶(hù)仍需要在云端訓(xùn)練 AI 模型,但可以通過(guò)在邊緣計(jì)算機(jī)上部署訓(xùn)練好的 AI 模型,在現(xiàn)場(chǎng)執(zhí)行數(shù)據(jù)收集和推理。本文討論如何為工業(yè) AIoT 應(yīng)用選擇合適的邊緣計(jì)算機(jī),并提供幾個(gè)案例研究以幫助入門(mén)。
將 AI 帶入 IIoT
工業(yè)物聯(lián)網(wǎng) (IIoT) 的出現(xiàn)使廣泛的企業(yè)能夠從以前未開(kāi)發(fā)的來(lái)源收集大量數(shù)據(jù),并探索提高生產(chǎn)力的新途徑。通過(guò)從現(xiàn)場(chǎng)設(shè)備和機(jī)械中獲取性能和環(huán)境數(shù)據(jù),組織現(xiàn)在可以使用更多信息來(lái)做出明智的業(yè)務(wù)決策。不幸的是,有太多的 IIoT 數(shù)據(jù)供人類(lèi)單獨(dú)處理,因此大部分信息都未經(jīng)分析和未使用。
因此,難怪企業(yè)和行業(yè)專(zhuān)家正在轉(zhuǎn)向 IIoT 應(yīng)用程序的人工智能和機(jī)器學(xué)習(xí)解決方案,以獲取整體視圖并更快地做出更明智的決策。
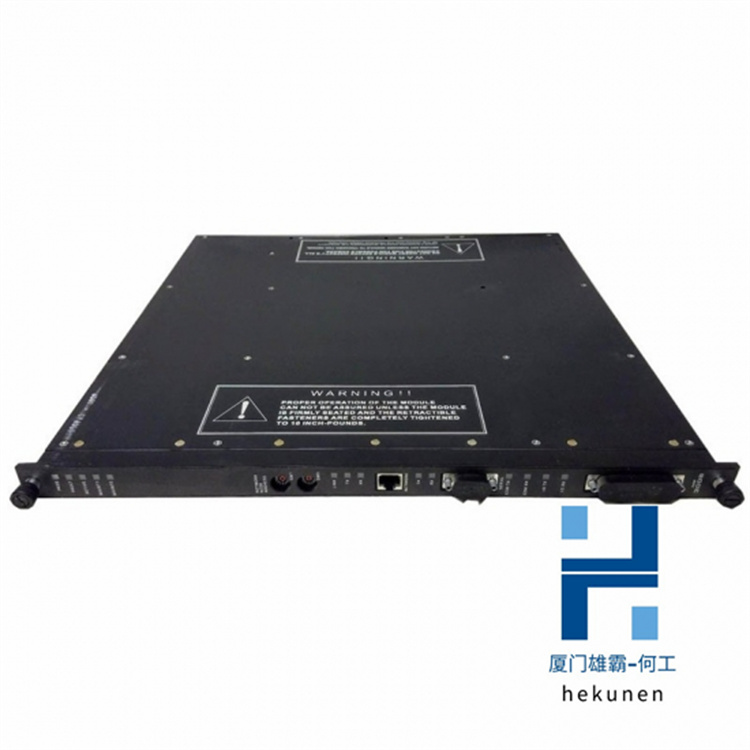
連接到互聯(lián)網(wǎng)的工業(yè)設(shè)備數(shù)量驚人地逐年增長(zhǎng),預(yù)計(jì)到 2025 年將達(dá)到 416 億個(gè)端點(diǎn)。更令人難以置信的是每臺(tái)設(shè)備產(chǎn)生的數(shù)據(jù)量。
事實(shí)上,手動(dòng)分析制造裝配線(xiàn)上所有傳感器生成的信息可能需要一生的時(shí)間。難怪“不到一半的組織結(jié)構(gòu)化數(shù)據(jù)被積極用于決策,而只有不到 1% 的非結(jié)構(gòu)化數(shù)據(jù)被分析或使用”。
對(duì)于 IP 攝像機(jī),每天生成的近 1.6 EB 視頻數(shù)據(jù)中只有 10% 得到分析。盡管我們有能力收集越來(lái)越多的信息,但這些數(shù)字表明數(shù)據(jù)分析存在驚人的疏忽。人類(lèi)無(wú)法分析我們產(chǎn)生的所有數(shù)據(jù)正是企業(yè)正在尋找將人工智能和機(jī)器學(xué)習(xí)納入其 IIoT 應(yīng)用程序的原因。
想象一下,如果我們每周 5 天,每天 8 小時(shí),僅依靠人類(lèi)視覺(jué)在制造裝配線(xiàn)上手動(dòng)檢查高爾夫球上的微小缺陷。即使公司能夠負(fù)擔(dān)得起一整支檢查員,每個(gè)人仍然自然容易疲勞和人為錯(cuò)誤。
同樣,鐵路軌道扣件的人工目視檢查只能在列車(chē)停止運(yùn)行后的半夜進(jìn)行,不僅耗時(shí)而且難度大。同樣,對(duì)高壓輸電線(xiàn)和變電站設(shè)備進(jìn)行人工檢查也會(huì)使人員面臨額外的風(fēng)險(xiǎn)。
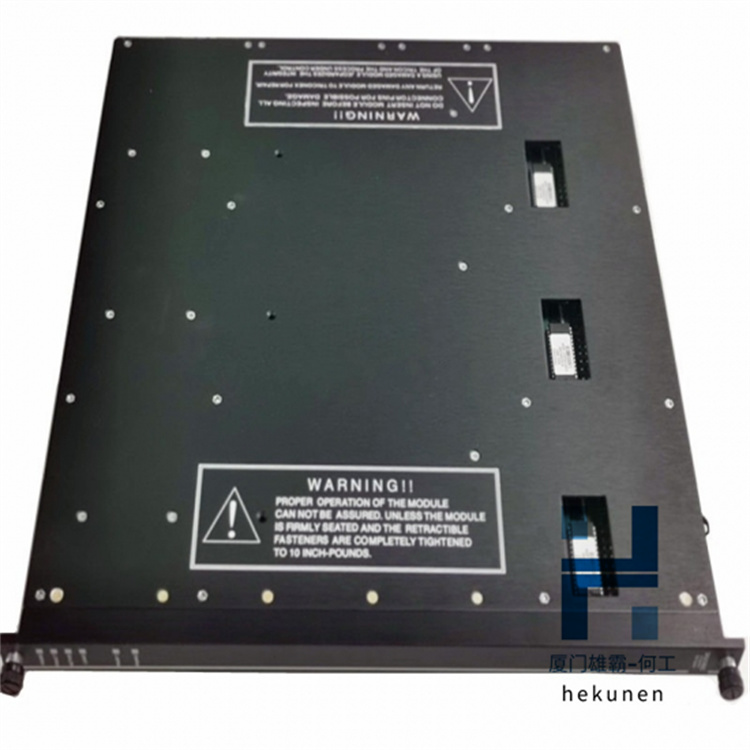
我司產(chǎn)品廣泛應(yīng)用于數(shù)控機(jī)械 冶金,石油天然氣,石油化工,
化工,造紙印刷,紡織印染,機(jī)械,電子制造,汽車(chē)制造,
塑膠機(jī)械,電力,水利,水處理/環(huán)保,市政工程,鍋爐供暖,能源,輸配電。
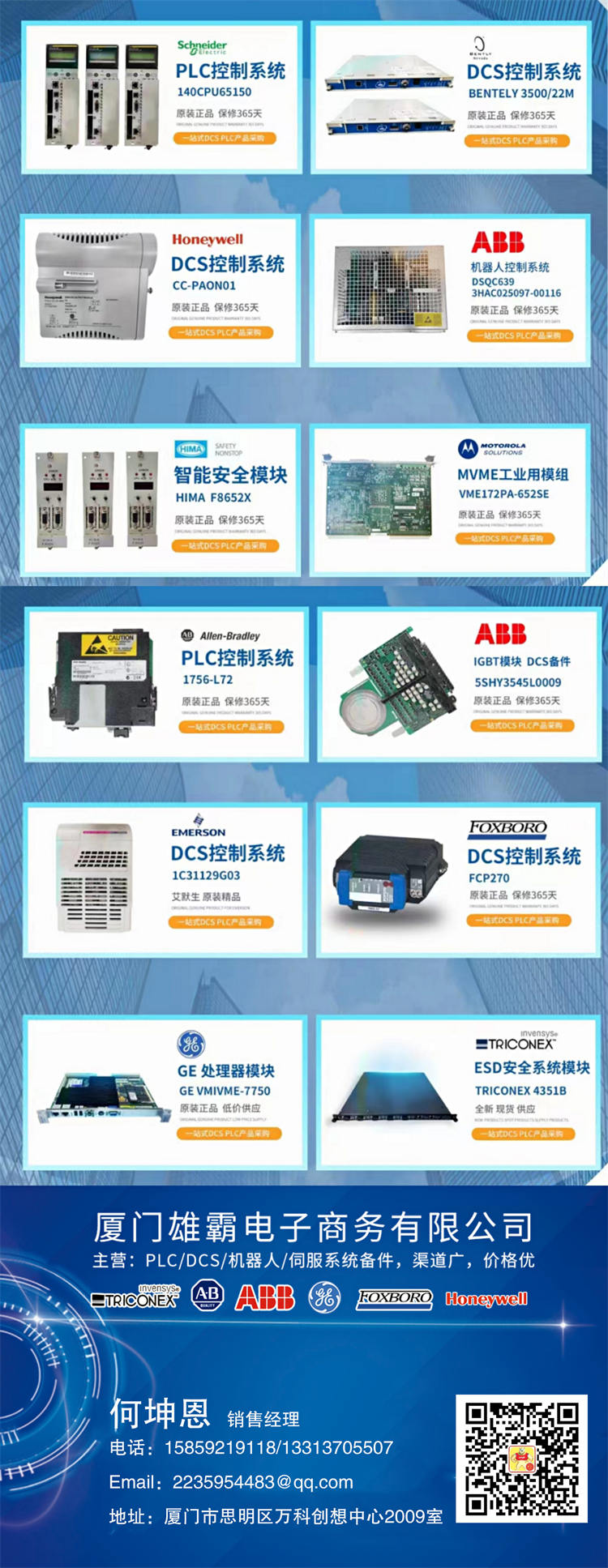
Enabling AI capabilities at the edge can improve operational efficiency and reduce risks and costs for industrial applications. Choose the right computing platform for your industrial AIoT application by addressing specific processing requirements during implementation.
IIoT applications are generating more data than ever before. In many industrial applications, especially highly distributed systems located in remote areas, constantly sending large amounts of raw data to a central server might not be possible. To reduce latency, reduce data communication and storage costs, and increase network availability, businesses are moving AI and machine learning to the edge for real-time decision-making and actions in the field.
These cutting-edge applications that deploy AI capabilities on IoT infrastructures are called the “AIoT.” Although users still need to train AI models in the cloud, data collection and inferencing can be performed in the field by deploying trained AI models on edge computers. This article discusses how to choose the right edge computer for industrial AIoT applications and provides several case studies to help get started.
Bringing AI to the IIoT
The advent of the Industrial Internet of Things (IIoT) has allowed a wide range of businesses to collect massive amounts of data from previously untapped sources and explore new avenues for improving productivity. By obtaining performance and environmental data from field equipment and machinery, organizations now have even more information at their disposal to make informed business decisions. Unfortunately, there is far too much IIoT data for humans to process alone so most of this information goes unanalyzed and unused.
Consequently, it is no wonder that businesses and industry experts are turning to artificial intelligence and machine learning solutions for IIoT applications to gain a holistic view and make smarter decisions more quickly.
IIoT data goes unanalyzed
The staggering number of industrial devices being connected to the Internet continues to grow year after year and is expected to reach 41.6 billion endpoints in 2025. What’s even more mind-boggling is how much data each device produces.
In fact, manually analyzing the information generated by all the sensors on a manufacturing assembly line could take a lifetime. It’s no wonder that “less than half of an organization’s structured data is actively used in making decisions, and less than 1% of its unstructured data is analyzed or used at all”.
In the case of IP cameras, only 10% of the nearly 1.6 exabytes of video data generated each day gets analyzed. These figures indicate a staggering oversight in data analysis despite our ability to collect more and more information. This inability for humans to analyze all of the data we produce is precisely why businesses are looking for ways to incorporate artificial intelligence and machine learning into their IIoT applications.
Imagine if we relied solely on human vision to manually inspect tiny defects on golf balls on a manufacturing assembly line for 8 hours each day, 5 days a week. Even if companies could afford a whole army of inspectors, each person is still naturally susceptible to fatigue and human error.
Similarly, manual visual inspection of railway track fasteners, which can only be performed in the middle of the night after trains have stopped running, is not only time-consuming but also difficult to do. Likewise, manual inspection of high-voltage power lines and substation equipment also exposes human personnel to additional risks.