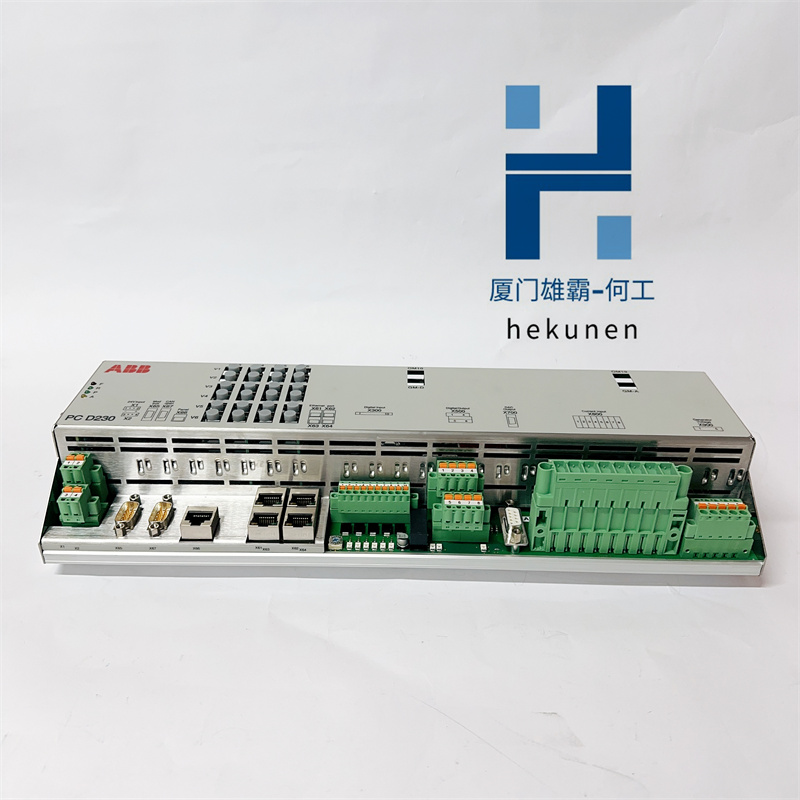
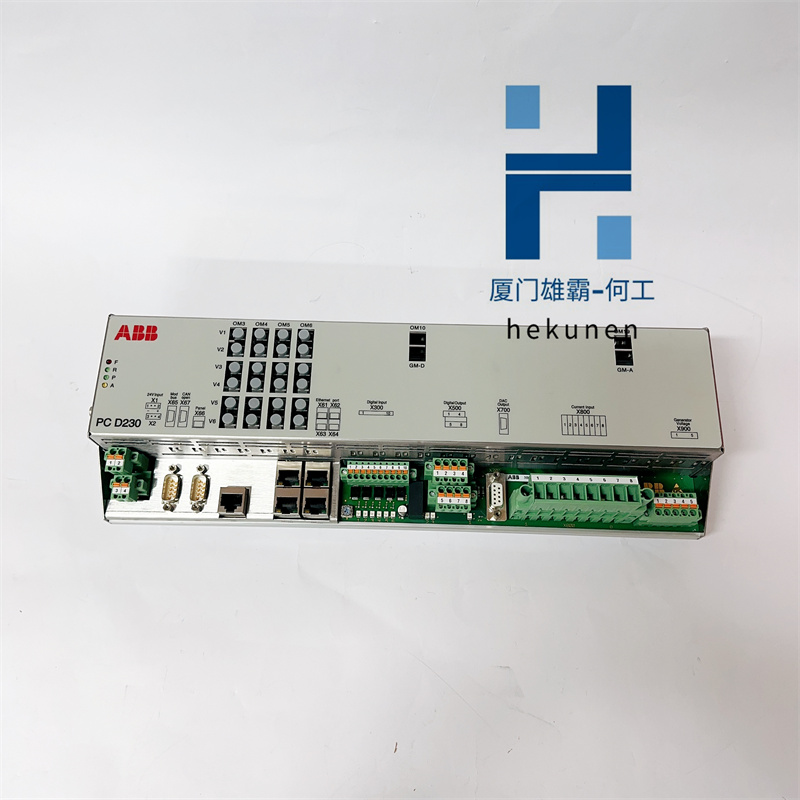
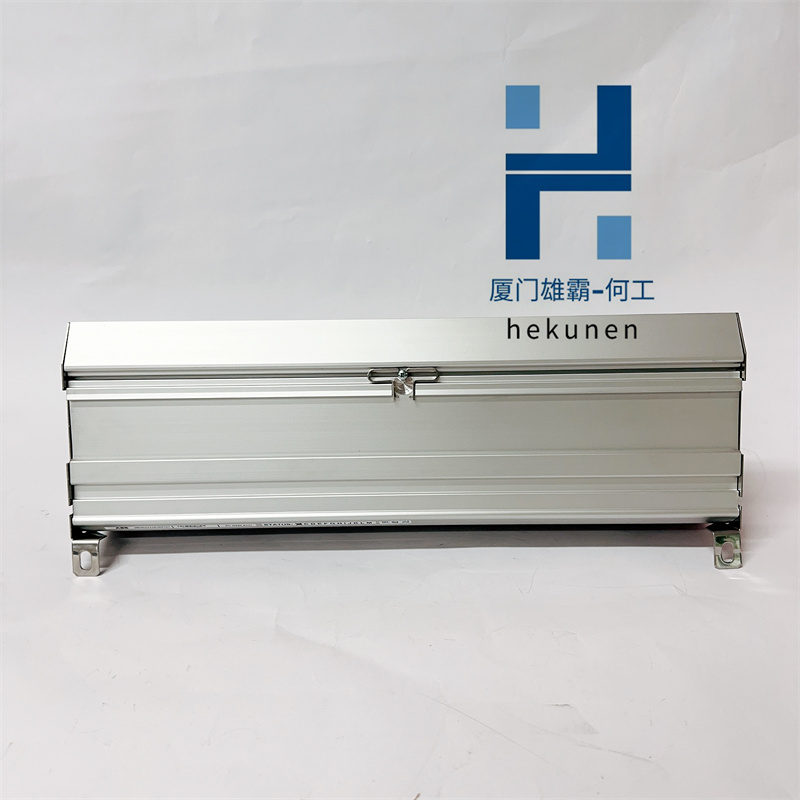
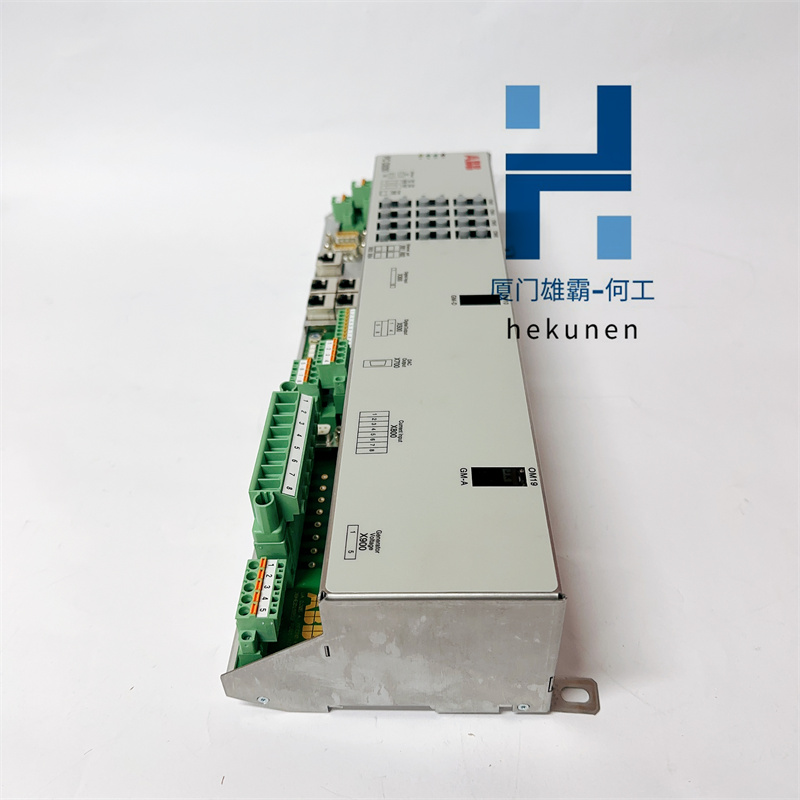
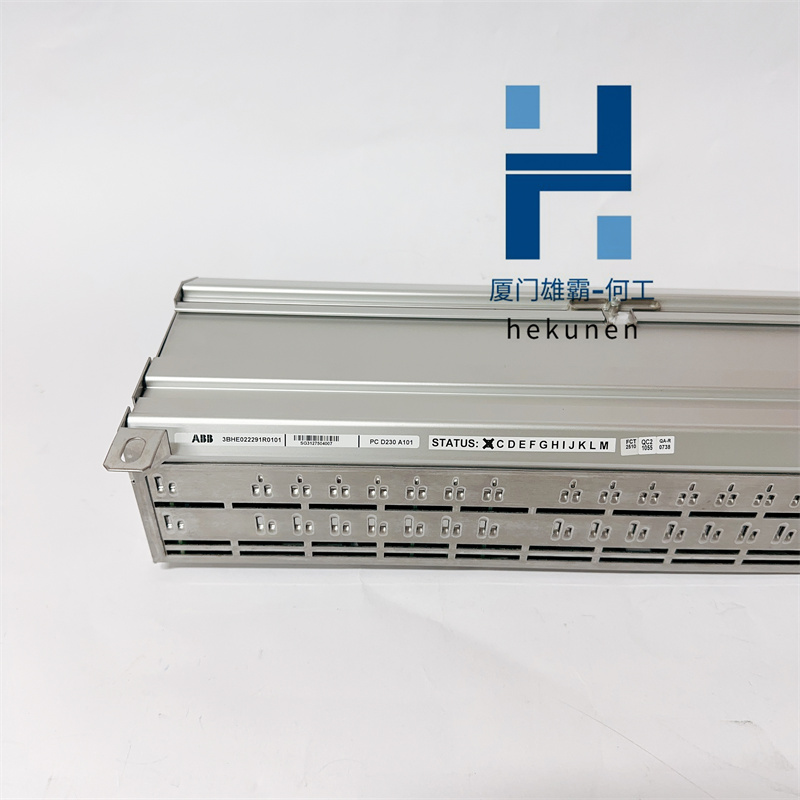
產(chǎn)品描述
這種緊湊的電路板是ABB工業(yè)逆變器驅(qū)動器的核心智能,可實現(xiàn)電機(jī)控制和高效的電源管理。
CPU是其核心:一個強(qiáng)大的處理器充當(dāng)板的命令中心,執(zhí)行復(fù)雜的控制算法,調(diào)整電機(jī)速度、扭矩和方向。
驅(qū)動器通信大師:與其他驅(qū)動器組件無縫交互,確保平穩(wěn)協(xié)調(diào)和性能。
保護(hù)本能:內(nèi)置安全措施可監(jiān)測關(guān)鍵參數(shù),防止過載、短路和其他潛在危險。
ABB的運(yùn)動控制專業(yè)知識:利用ABB在工業(yè)驅(qū)動技術(shù)方面數(shù)十年的經(jīng)驗,提供可靠高效的電機(jī)控制。
從復(fù)雜的算法到保護(hù)措施,該板確保ABB的逆變器驅(qū)動器為廣泛的工業(yè)應(yīng)用提供可靠的電力。
其他屬性
系列:Advant DCS/800xA
原產(chǎn)國:德國/瑞典/芬蘭
交付周期:庫存
ABB的庫存熱點項目
3BHB003154R0101 3bhl0003389p0104 5SHX2645L0004 3bhb0195r0124
3BHE009681R0101 3bhb 012961r0001 5SHX2645L0002 XVC724BE102 3bhe009 017r0102
3BHE009681R0101 3bhb01308r0001 5SHY3545L0010 UNS3020 HIEE205010R0003
3BHE022333R0101 5SHX0660R0002 5SXE05-0158 3BHE003855R0001/UNS 2882A-P,V1
3bhb 005171r0101 3bhl 000986p3105 5SHY3545L0002 3bhe 009319r0001/UNS 2881B-P,V1
AC10272001R0101 5SXE10-0181 5SHY6545L0001 3he009949r0002/UNS 4881B,V2
3bhb 003387r0101 3bhl 00385p0101 5SHX0845F0001 3bhe 014967r0002/UNS 2880B-P,V2
3bhb 003386r0101 3bhl 000387p0101 5SHX1445H0002 UFC765AE102 3bhe 003604r0102
AC10272001R0101/5SXE10-0101/5SHY55L4500 XVC767AE105 3BHB007209R0105
AC10272001R0101/5SXE10-0101/5SHY55L4520 XVC768115 3BHB0072R115
3bhb0003230r0101 3bhl0003392p0101 5SHX1060H0001 XVC768115 3bhb0007211r115
3bhb 003387r0101 3bhl 000385p0101 5SHX0845F0001 AFC094AE02 HIEE200130R0002
5SXE10-0181 5SHY55L4520 AC10272001R0101 ARC093AE01 HIEE300690R0001
我們的主營品牌
-ABB Advant-800xA、Advant OCS、Bailey Infi 90和Net 90、H&B Freelance 2000、DSQC機(jī)器人、IGCT/IIGBT
-GE通用電氣、Genius I/O、QuickPanel、RX3i PacSystem、90系列、90系列和VersaMax系列
-Allen-BradleyAllen-Bradley SLC500,MicroLogix,CompactLogix,ControlLogix,PLC-5,面板視圖,
-Bently Nevada 3300系統(tǒng)、3500系統(tǒng)
-霍尼韋爾7800系列、FSC、IPC、Mxopen、TDC 2000、TDC 3000、Experion PKS(C200、C300)
-橫河Centum CS-Centum VP,Centum XL-micro XL,F(xiàn)A-M3,ProSafe PLC
-Ovation、Foxboro、EPRO、Emerson DeltaV、富士、HIMA、Prosoft、Invensys Triconex、ICS TRIPLEX、Woodward、Bachmann、Schneider
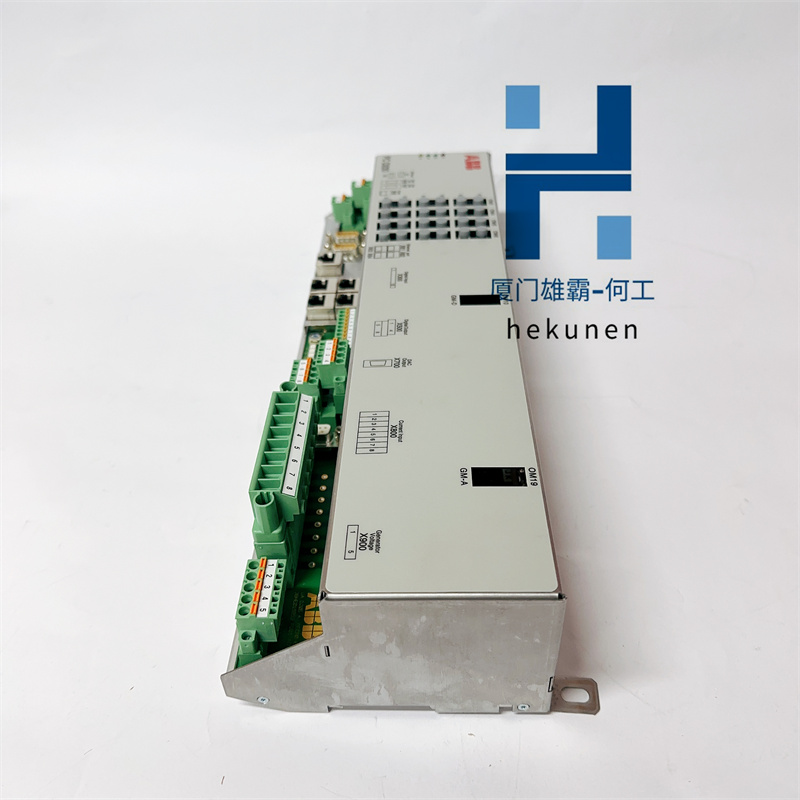
Shaft current is one of the common problems in high-voltage motors, generators, variable frequency motors, and other types of motors. When the shaft current is high, it can cause the bearing system of the motor to collapse, even affecting the motor winding. Therefore, the control of shaft current is a common concern for motor manufacturers and even users.
A netizen suggested that he detected the shaft voltage and asked if it is possible to measure the shaft current? We will have a brief discussion on whether shaft voltage will harm the bearing system of the motor and other related issues.
From the analysis of the principle of current formation, shaft voltage and closed circuit are necessary conditions for generating shaft current. The measures to avoid shaft current are based on two ideas: cutting off the circuit or bypassing it.
If circuit breaking measures such as insulated bearings, insulated end caps, and insulated bearing sleeves are used in the design and manufacturing process of the motor, even if the shaft voltage exists, because no closed circuit can be formed, the shaft current will naturally not be generated.
If a bypass measure is adopted, that is, guiding the direction of shaft current through grounded carbon brushes, it can greatly reduce the magnitude of shaft current and naturally solve the problem of shaft current harm to bearings.
We are now discussing another issue, which is raised by the netizen. When the shaft voltage is high, it will pose a threat to the quality and performance of bearings. Therefore, necessary measures need to be taken when the shaft voltage is high! According to the accumulation and statistics of data from different motor manufacturers, when the shaft voltage generated by the motor does not exceed 350mV, it does not have a significant impact on the bearing system of the motor. Otherwise, corresponding avoidance measures must be taken.
Finally, let's talk about the detection of shaft voltage and shaft current. Relatively speaking, the detection of shaft voltage is relatively simple, and can be detected using a millivolt meter with appropriate accuracy. However, due to the irregularity of the shaft current passing through the channel, the collection of shaft current is relatively difficult, and specialized detection equipment is needed for detection.
The shaft current monitoring device adopts a high-performance microcontroller as the core control component to form a controller, and a hollow ring transformer as the shaft current sensor to monitor the changes in motor shaft current. The microcontroller monitors the real-time change value of the shaft current sensor, which is linearly related to the large shaft current. After filtering and numerical transformation, it is confirmed that the shaft current exceeds the set value. The shaft current monitoring device outputs a second level alarm signal. The device displays the specific current size in real-time through parameter tuning.
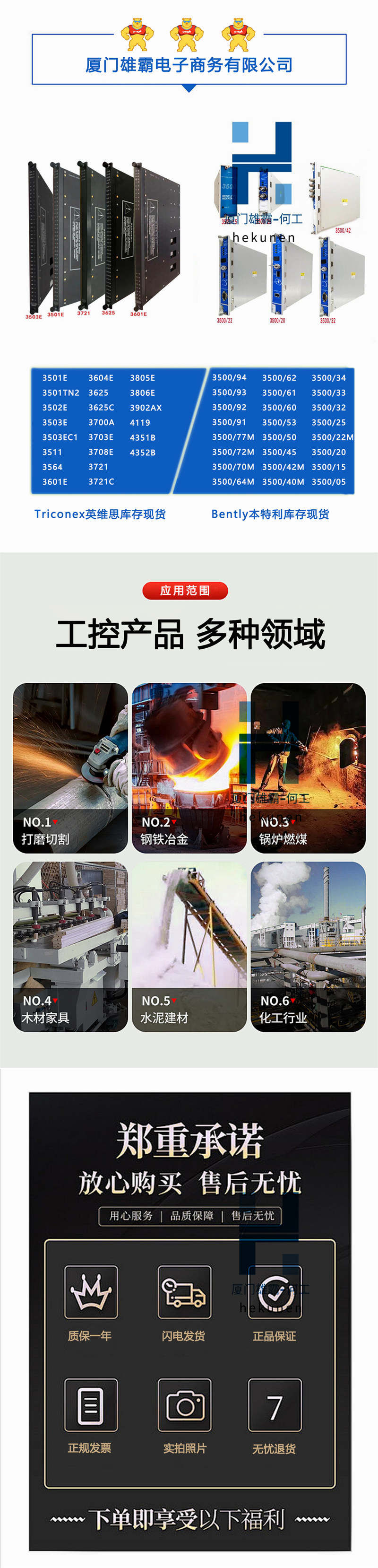