軸電流,是高壓電機(jī)、發(fā)電機(jī)、變頻電機(jī)等類型電機(jī)比較常見的問(wèn)題之一,軸電流較大時(shí),會(huì)導(dǎo)致電機(jī)的軸承系統(tǒng)發(fā)生崩潰,甚至波及到電機(jī)繞組,因而,軸電流的控制,是電機(jī)生產(chǎn)廠家乃至電機(jī)使用者共同關(guān)切的問(wèn)題。
有網(wǎng)友提出,他檢測(cè)到了軸電壓,問(wèn)是否可以測(cè)出軸電流?軸電壓是否會(huì)危害到電機(jī)的軸承系統(tǒng)等問(wèn)題,針對(duì)該問(wèn)題,我們與大家進(jìn)行一個(gè)簡(jiǎn)單交流。
從電流形成的原理分析,軸電壓和閉合回路,是產(chǎn)生軸電流的必要條件,軸電流的規(guī)避措施,就是圍繞切斷回路或旁路的兩個(gè)思路展開。
如果在電機(jī)的設(shè)計(jì)和制造過(guò)程中,采用了諸如絕緣軸承、絕緣端蓋、絕緣軸承套等斷路措施,盡管軸電壓存在,因?yàn)闆](méi)有能形成閉合回路,自然也就不會(huì)產(chǎn)生軸電流。
如果是采用旁路措施,即,通過(guò)接地碳刷,將軸電流的走向進(jìn)行引導(dǎo),既可大大減小軸電流的大小,自然也就解決了軸電流對(duì)軸承的危害問(wèn)題。
軸電流監(jiān)測(cè)裝置采用高性能單片機(jī)為核心控制部件構(gòu)成控制器,采用空心環(huán)形互感器為軸電流傳感器,監(jiān)測(cè)電機(jī)軸電流變化。單片機(jī)實(shí)時(shí)監(jiān)測(cè)軸電流傳感器的變化值,該數(shù)值與大軸電流呈線性變化關(guān)系,經(jīng)濾波、數(shù)值變換處理后,確認(rèn)軸電流超過(guò)整定值后,軸電流監(jiān)測(cè)裝置輸出二級(jí)報(bào)警信號(hào)。裝置通過(guò)參數(shù)整定、實(shí)時(shí)顯示具體的電流大小。
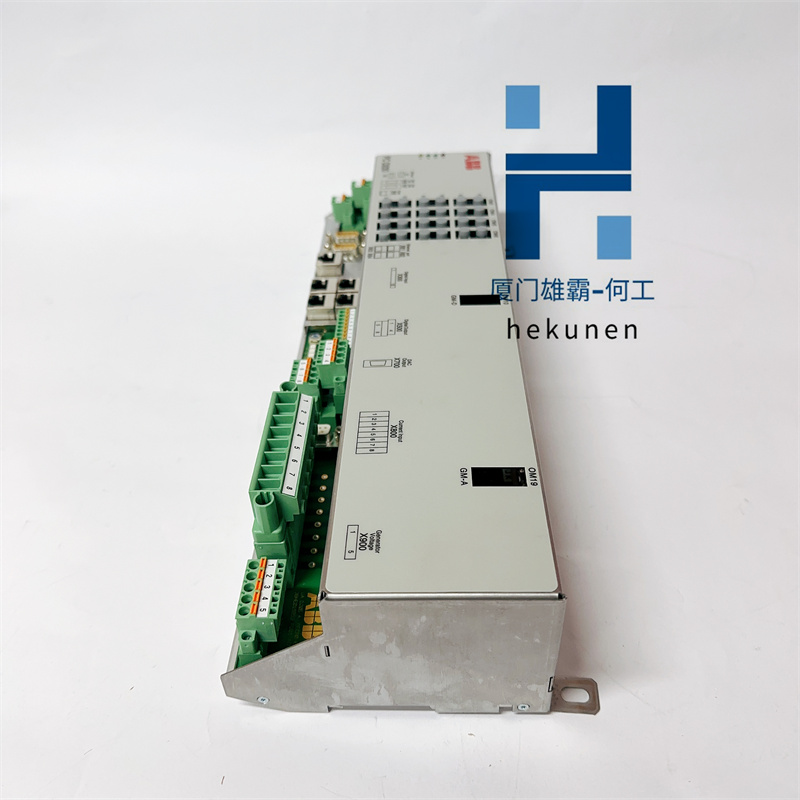
Shaft current is one of the common problems in high-voltage motors, generators, variable frequency motors, and other types of motors. When the shaft current is high, it can cause the bearing system of the motor to collapse, even affecting the motor winding. Therefore, the control of shaft current is a common concern for motor manufacturers and even users.
A netizen suggested that he detected the shaft voltage and asked if it is possible to measure the shaft current? We will have a brief discussion on whether shaft voltage will harm the bearing system of the motor and other related issues.
From the analysis of the principle of current formation, shaft voltage and closed circuit are necessary conditions for generating shaft current. The measures to avoid shaft current are based on two ideas: cutting off the circuit or bypassing it.
If circuit breaking measures such as insulated bearings, insulated end caps, and insulated bearing sleeves are used in the design and manufacturing process of the motor, even if the shaft voltage exists, because no closed circuit can be formed, the shaft current will naturally not be generated.
If a bypass measure is adopted, that is, guiding the direction of shaft current through grounded carbon brushes, it can greatly reduce the magnitude of shaft current and naturally solve the problem of shaft current harm to bearings.
We are now discussing another issue, which is raised by the netizen. When the shaft voltage is high, it will pose a threat to the quality and performance of bearings. Therefore, necessary measures need to be taken when the shaft voltage is high! According to the accumulation and statistics of data from different motor manufacturers, when the shaft voltage generated by the motor does not exceed 350mV, it does not have a significant impact on the bearing system of the motor. Otherwise, corresponding avoidance measures must be taken.
Finally, let's talk about the detection of shaft voltage and shaft current. Relatively speaking, the detection of shaft voltage is relatively simple, and can be detected using a millivolt meter with appropriate accuracy. However, due to the irregularity of the shaft current passing through the channel, the collection of shaft current is relatively difficult, and specialized detection equipment is needed for detection.
The shaft current monitoring device adopts a high-performance microcontroller as the core control component to form a controller, and a hollow ring transformer as the shaft current sensor to monitor the changes in motor shaft current. The microcontroller monitors the real-time change value of the shaft current sensor, which is linearly related to the large shaft current. After filtering and numerical transformation, it is confirmed that the shaft current exceeds the set value. The shaft current monitoring device outputs a second level alarm signal. The device displays the specific current size in real-time through parameter tuning.
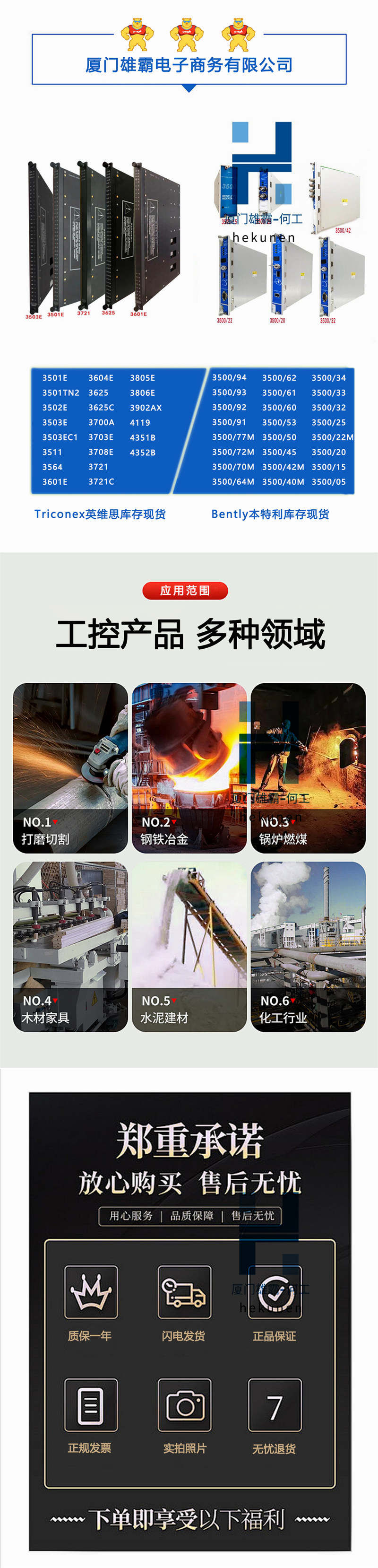